Food Industry
We have done quite a few interesting projects for the food industry, from cheese processing plants, to fruit packaging, to high-tech potato chip manufacturing (outside of silicon valley).

We used strain gages to estimate strain levels in a large processing plant that runs at low vacuum pressure. The system was experiencing cracks in the stainless steel vessels that would shut down production, this was a very high priority issue.

Something in the plant was thought to have changed resulting in the formation of cracks at two locations. These locations were close to where we would expect high stress due to large stiffness changes in the structure. We wanted to help distinguish what part of the process cycle produced the most strain and what was causing the presumably large strain levels.
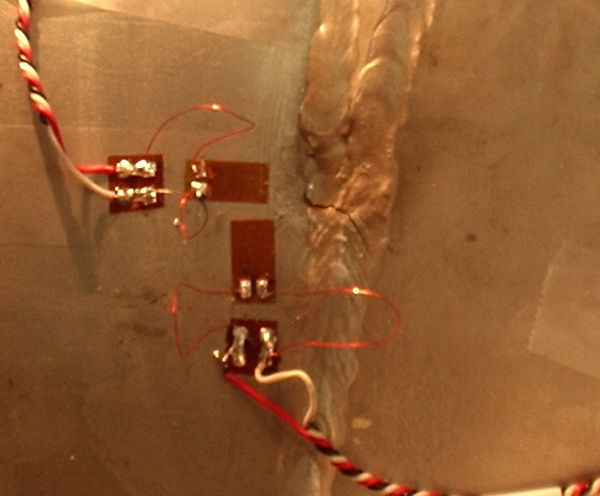
We used vibration sensors as well as strain gages to characterize the disturbances and the system response during the process cycle that lasted many hours.

Engineering parameters used in a very rough estimate of a fatigue limit
The dynamics forces from the fans were suspected of contributing to the new cracks in the vacuum system. The strain measurement, however, showed that the AC strain was very low.

The static strain, however, was very large in the axis perpendicular to the crack, significantly exceeding the fatigue limit.


This project goes down as one of our toughest as it involved soldering tiny strain gage wires in low light on top of a 130 degree vacuum tank in the early hours of the morning. Henceforth, we come to new projects in industrial settings prepared with strain gages with pre-soldered lead wires and quality headlamps. We have learned many valuable lessons in vibration testing and have developed novel approaches that have saved considerable time and effort. Bringing delicate instrumentation into an industrial setting, installing sensors, running cable, and setting up meaningful experiments requires logistical techniques that can only be developed with experience. We have been learning these lessons for the past 30 years and continue to refine our techniques.
​
We identified an issue with the structure and the process, helped the engineers at the plant understand the problem, proposed several solution options, and designed modifications.